2.2
Auxiliary materials
Auxiliary or helping materials are those materials used in the dental laboratory to make aids necessary for the creation of prostheses.
Definition
Auxiliary materials do not become a part of restorations, yet they are absolutely essential for their manufacture, from the beginning to the end.
We can classify materials according to the purpose for which they are used (the same material can fall into several groups) into these six groups of materials: impression, model, modelling, investment, abrasion and polishing, and insulating.
2.2.1
Impression materials
Dental lab technicians typically start their work when they receive an impression of a patient's oral cavity situation from the dentist's office. The dentist prepares the relevant part of the cavity and then uses an impression material of their choice to capture the situation accurately (makes a negative imprint) for the technician who subsequently creates its model (a positive reproduction).
Since the whole production of a prosthesis depends on the accuracy of the impression, materials used to make it should meet the following requirements: sufficient firmness and elasticity, high volume accuracy, favourable capturing ability, biocompatibility, taste and smell, compatibility with model materials. Suitable impression materials may be divided into two groups, according to what agent sets, or solidifies, them: thermoplastic materials and chemoplastic materials.
Thermoplastic materials can be divided further into rigid and flexible materials according to the state in which they are removed from the mouth. Impression compounds and impression wax are rigid. Agar (hydrocolloid) materials are flexible.
Chemoplastic materials can also be grouped as rigid and flexible. Rigid materials include plaster and zinc-oxide eugenol paste. Flexible materials comprise alginate (hydrocolloid) materials and elastomers – silicone, polysulphide, polyether. Silicone elastomers, which are the most frequently used in the group, are further divided into silicone rubbers cured by addition or condensation.
+
Fig. 6. Thermoplastic shellac and chemoplastic alginate
+
Fig. 7. Silicone impression materials
2.2.2
Model materials
After receiving an impression from the dentist's office, the technician needs to create a positive model from the impression (hence model materials). Unfortunately, impressions are never absolutely accurate.
Disadvantage
Moreover, model materials have issues of their own. Specifically, we talk about the expansion of the most commonly used model material – plaster.
Consequently, the situation model is larger than the actual situation it tries to capture. Obviously, technicians will do all they can to take this into account. Still, they should also strive to choose materials that provide the most accurate results. Such materials would meet a number of characterics, e.g. sufficient dimensional stability, resistance to abrasions, ease of use, sufficient bending, breaking strength, and compatibility with other materials.
The only material which fits the requirements and is commonly used nowadays is plaster (gypsum). Its chemical name is calcium sulfate dihydrate.
Interesting
Gypsum is mined in various locations around the world. It is dehydrated, purified, sometimes calcined and sold as a hemihydrate powder.
There are various types of plaster used in the lab, but the principle remains the same. Gypsum powder is mixed with water in a given proportion (water/powder ratio). The technician then uses the mixture to give it a new shape before it sets.
There are five types of plaster (the fifth type has been included recently):
- type I (so called impression plaster) has been replaced by less rigid materials.
- type II (dental plaster) is of natural white colour and is used mostly for study situation models, but also to fix models in articulators and for other purposes.
- type III (dental stone) is used for opposite models, situation models for complete dentures and for less complicated partial removable dentures.
- type IV (dental/die stone, high strength) is used to make fixed prostheses and metal constructions of removable prostheses.
- type V (dental stone, high strength, high expasion) is suitable when making work models for the production of inlays, onlays and complex fixed bridges from base metal alloys.
+
Fig. 8. Models made of different plaster types
2.2.3
Modelling materials
Modelling materials are used to model the actual prosthesis. The prosthesis model has to correspond, in its shape and dimensions, to the future prosthesis. Therefore, the most important requirement for such materials is the ease with which they soften to a plastic state. Once plastic, they can be formed into various shapes required by different types of dental prostheses. After modelling, they should also be able to keep their shape and dimensions. It is also crucial that they may be burned completely or washed out during the following production steps. Finally, their colour should easily distinguish them from the work situational model.
It is dental waxes that best fit the demands mentioned above. Dental wax is a mixture of two or more waxes with other additives. Waxes used in the mixture can be natural or synthetically made (eg. synthetic paraffin, polyglycols, polyethylens – usually bearing brand names). Natural waxes are of animal (eg. beeswax), plant (eg. carnauba wax) or mineral origin (paraffin, ozokerite). Additives used in dental waxes are blended in to achieve the desirable working characteristics. They include gums, oils, fats, fatty acids, and resins. Modelling waxes are composed of paraffin, beeswax and resin.
+
Fig. 9. Modelled wax teeth set in a plaster model
Note
Dental waxes are not used solely for modelling. They are used in different procedures and have different properties and names typically associated with these procedures (inlay wax, casting wax, boxing wax, sticky wax, utility wax).
Table 3. Vocabulary Table No. 3
English | Czech | English | Czech |
aids | pomůcky | purpose | účel |
impression | otisk, otiskovací | capture | zachytit |
requirements | požadavky | issues | problémy |
plaster | sádra | bending | ohyb |
purified | přečištěná | calcined | kalcinovaný |
set | ztuhnout | soften | změkčit |
distinguish | odlišit | waxes | vosky |
brand names | obchodní názvy | plant | rostlinný |
blended in | zamíchány |
This interactive object cannot be incorporated into the material.
Click HERE to see the object.
Click HERE to see the object.
Interactive object 3. Follow the instruction and complete the exercises (the user will be directed to an external page). It is possible to set several options for the exercise in the Options menu on the left side of the screen.
2.2.4
Investment materials
Investments are materials that are used to wrap the wax pattern, wholly or partially, and are then burnt out or washed out to remove the wax. The resulting form, or mould, is used to cast molten metal or alloy, or to press (cast) plastic that forms the prosthesis itself.
From the above description, it follows naturally that investment materials should have these characteristics: perfect adhesion to the surface of the wax model, sufficient strength to withstand molten metal (after burning), absence of harmful substances that could negatively affect the main material of the prosthesis. Moreover, it should enable gases to escape the mould. It should also permit easy divestment of the cast. Finally, it should allow for a degree of expansion to compensate for casting contraction.
Investment materials consist of two primary substances that, together with certain additives, meet all the requirements listed above. The first substance is a refractory material, a form of silicon dioxide (quartz/fused quartz, tridymite, cristobalite). The second substance is a binder that helps silicion dioxide to form a coherent solid mass. There are three types of binder: gypsum, phosphate and ethyl silicate. Gypsum materials are suitable for casting gold alloys at temperatures of up to 700 °C. Phosphate bonded investments create moulds for high temperature casting (metal-ceramic, cobalt-chromium alloys). Ethyl silicate materials have a limited use, principally in the casting of base metal alloys for partial dentures.
+
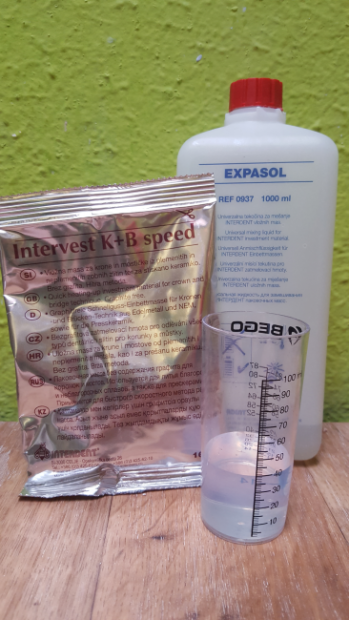
Fig. 10. Phosphate investment material and mixing liquid
+
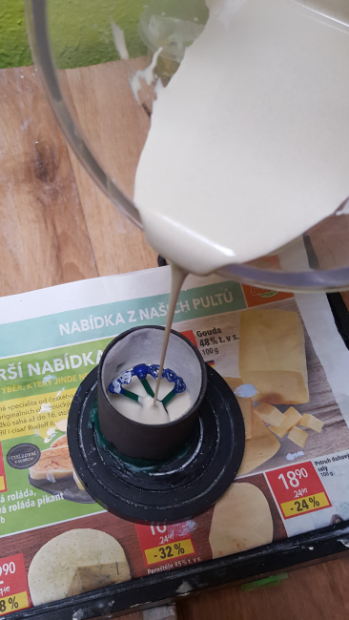
Fig. 11. Investment being poured into a casting ring
2.2.5
Abrasion and polishing materials
Before a prosthesis is sent back to the dentist, it has to be finished by abrasion and polishing. These two procedures bring high esthetic results, oral hygiene and function to patients and prolonged life of restorations.
Abrasion removes coarser surface irregularities. It removes excess material by cutting or grinding materials by means of abrasives. As a result, anatomical form is achieved in the prosthesis. Abrasives must be harder than the substrate (the prosthesis).
Example
They include, for example, diamond (natural or artificial), carbide (tungsten, silicone), emery, and quartz.
Polishing into high gloss is the final stage of prostheses preparation. Polishing materials are (very) fine. Powders and pastes used for polishing are made of materials such as pumice, chalk, diamond powder, ferrous and chromium oxides, and electrolytic polymers.
+
Fig. 12. Abrasion and polishing materials and aids
2.2.6
Insulating materials
Insulating materials are the means that separate two substances in order to prevent them from joining or affecting each other adversely. For example, they prevent moisture from entering plastics during polymerization or modelling wax from sticking to work models.
These examples also show that they are not used at the end of prosthesis manufacture. Rather, they are used in various stages of the manufacturing process whenever an interaction of two substances would be undesirable.
Insulating materials (separating media) include: cold water, detergent, separating solution, alginate solution, talcum, tin foil, (silicone) separating agent, cellophane foil, platinum foil, and degreasing solution.
+
Fig. 13. Examples of insulating materials
Table 4. Vocabulary Table No. 4
English | Czech | English | Czech |
investments | formovací hmoty | wrap | obalit |
mould | forma | molten | roztavený |
adhesion | přilnutí | surface | povrch |
affect | ovlivnit | gases | plyny |
divestment | vyjmutí | refractory | žáruvzdorný |
polishing | leštící, leštění | coarser | hrubší |
excess | přebytečný | grinding | broušení |
emery | smirek | gloss | lesk |
pumice | pemza | chalk | křída |
adversely | nepříznivě | sticking | přilepení se |
undesirable | nežádoucí | detergent | saponát |
solution | roztok | foil | fólie |
degreasing | odmašťovací |
©
For licensing reasons, this interactive object cannot be directly incorporated into the material. Click HERE to see the object.
Interactive object 4. Make the words disappear by putting the same Czech and English words onto each (the user will be directed to an external page). Do it as quickly as possible.
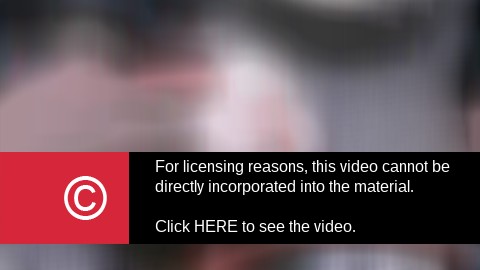
Video 2. How it’s made – false teeth
©
For licensing reasons, this interactive object cannot be directly incorporated into the material. Click HERE to see the object.
Interactive object 5. Set the options first and then translate the words on the asteroids before they hit you (the user will be directed to an external page).